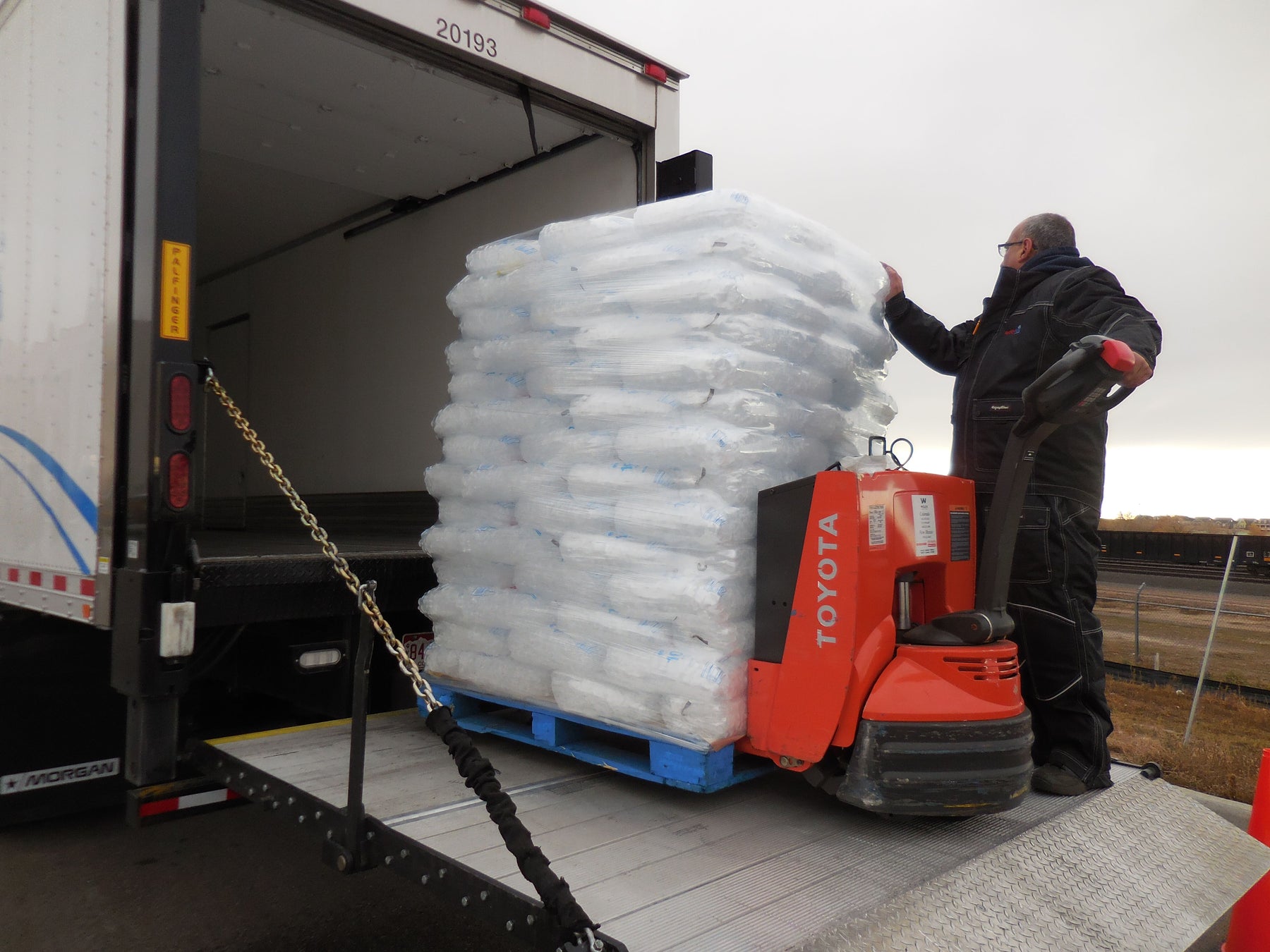
Create a Forklift Hazard Control Checklist
As an experienced manager or operations professional, you understand a busy warehouse or distribution center can be rife with potential—often hidden—hazards. And you may also know forklift accidents rank high on the list of items leading to worker injury. In fact, many industries list forklift tip-over as the leading cause of employee death in the materials handling arena. Once an accident takes place, you can take steps to prevent a similar event from taking place under similar conditions; for example, after a tip-over results from insufficient training, you can improve your training program.
But why not get ahead of these incidents and take steps to prevent these hazards before they result in real harm? Create a checklist similar to the one below and adapt it to the needs of your workplace. Then review your checklist annually to make sure you’re keeping potential incidents and accidents under control.
Hazard Control Checklist
Forklift use and maintenance hazards:
1. Employees do not receive adequate training or would like to receive more training than your current program provides. (Y/N)
2. Employee actions in the workplace are often influenced by speed and stress. (Y/N)
3. Forklifts receive routine maintenance fewer than three times per year. (Y/N)
4. Forklifts are not replaced until they fail to function. (Y/N)
Operator control and communication hazards:
5. Operators do not routinely use warnings, lights and signals. (Y/N)
6. Managers have observed at least one incident of reckless behavior, such as pedestrians standing under elevated forks or riding on forks. (Y/N)
7. Communication between workers is occasionally strained, unclear or unreliable.
8. Operators allow maintenance concerns to go unreported, or fear reporting problems to management. (Y/N)
9. Forklifts have been observed in improperly parked positions. (Y/N)
Workplace design hazards:
1. Are workplace aisles to narrow for comfortable and safe forklift navigation? (Y/N)
2. Have any obstructions been noted at doors, at intersections or within aisles? (Y/N)
3. Are forklifts used in working areas or areas with high volumes of pedestrian traffic? (Y/N)
4. Do floor surface materials, conditions and elevations change throughout the workplace? (Y/N)
5. Do any of the following environmental hazards ever appear in the workplace: dust, insufficient lighting, high noise levels, temperature extremes? (Y/N)
6. Are pallets in the workplace poorly stacked or in poor repair? (Y/N)
Business owners and operations managers should tour the facility and review this checklist on an established, regular schedule. Any hazards that warrant a “yes” response should be addressed immediately, well before any dangerous incidents occur.
For more on how to keep your workplace safe and your forklifts in good repair, contact the materials handling experts at Liftow.
Leave a comment